Hardware-in-Loop Testing: In the ever-evolving fields of engineering and technology, the development of complex systems necessitates extensive testing to guarantee performance, functionality, and safety.
Hardware-in-the-loop (HIL) testing is one important testing technique that has gained popularity in several industries, including automotive, aerospace, and industrial automation.
Electronic control units (ECUs) use embedded software; the primary test method for this is Hardware-in-loop testing. It allows actual ECUs to be tested in a controlled setting.
The reproducibility and automation of these hardware-in-the-loop simulation tests enable round-the-clock thorough testing in the lab, reduce validation times, and expand the set of possible Hardware-in-loop test possibilities.
According to Verified Market Report, Hardware-in-the-loop Market size was valued at USD 100.00 Million in 2023 and is expected to reach USD 150.00 Million by the end of 2030 with a CAGR of 5.99% during the forecast period 2024-2030.
The Hardware-in-the-Loop (Hardware-in-loop) market is a subset of the broader simulation and testing technologies industry, mostly utilized in the development and verification stages of complex electronic control systems.
The Hardware-in-the-Loop (Hardware-in-loop) industry is experiencing significant growth due to the increasing complexity of automotive systems.
To progress in autonomous driving and electric car development, LiDAR, Battery Management Systems (BMS), and other essential components need to be put through a rigorous testing process.
To ensure security and promote innovation in the automotive industry, Hardware-in-loop simulation provides a secure and efficient framework for evaluating these systems in a range of simulated scenarios.
This blog explores a variety of topics, including hardware-in-loop testing, its functions, benefits, difficulties encountered when testing automotive systems, and more.
What is Hardware-In-Loop (Hardware-in-loop) testing?
Hardware-in-the-loop (Hardware-in-loop) testing is, to put it simply, a testing methodology used in real-time embedded controller development that shortens development times and increases test efficacy.
Electronic Control Unit (ECU) functions can be tested in a simulated environment with Hardware-in-loop testing, which validates software without requiring the actual vehicle system.
Automotive software’s functionality, system integration, and communication are all validated by Hardware-in-loop testing.
Due to their complexity, ECUs require many combination testing to guarantee response and functionality.
Advanced algorithms, for instance, are used by advanced driver-assistance systems (ADAS) to process data in real-time from many sources.
This can include any device that helps drivers avoid probable mistakes in judgment, such as radars, cameras, global positioning systems (GPS), and sensors.
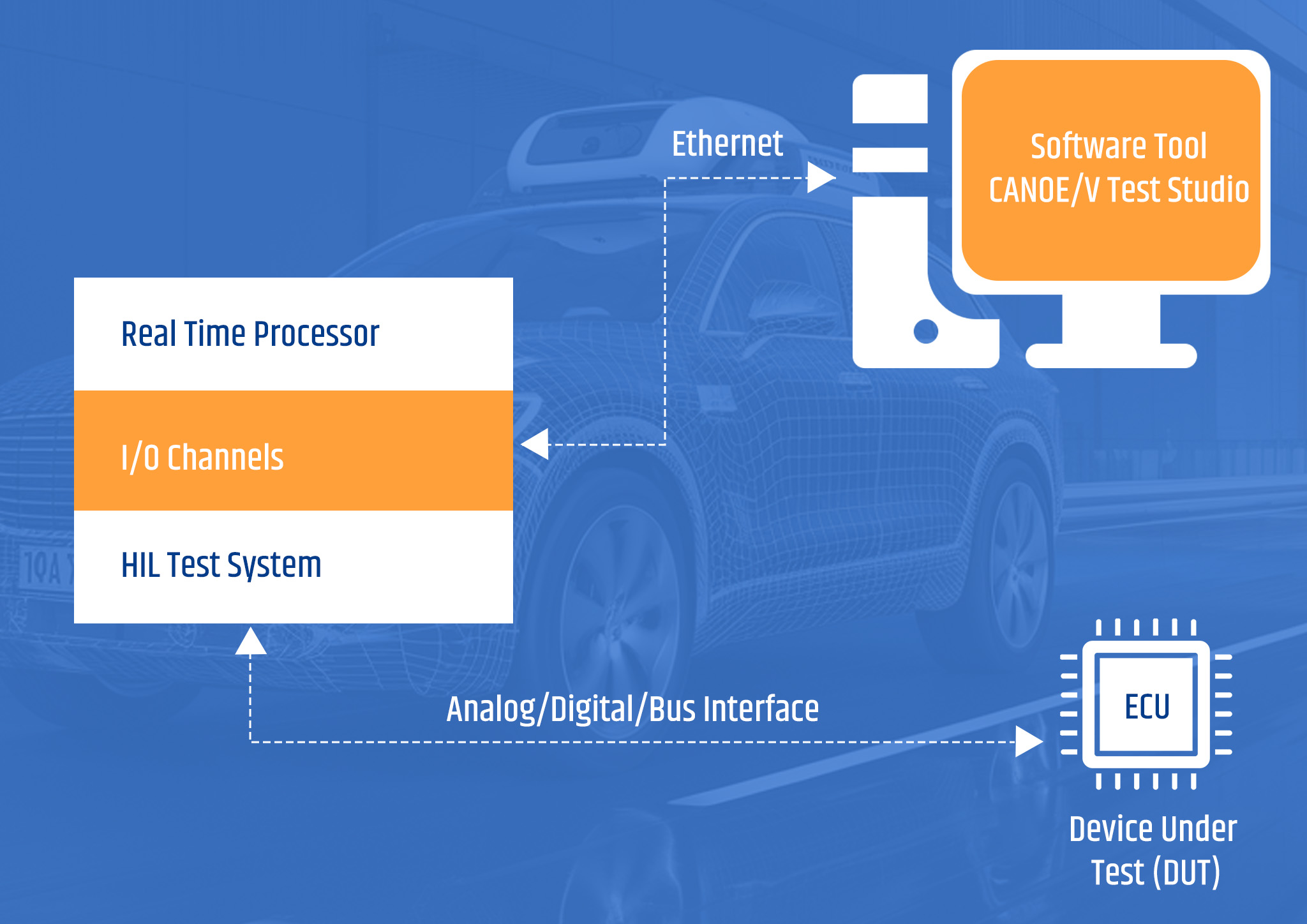
Hardware-in-Loop Testing Architecture
How Does the Hardware-in-Loop Testing Process Work?
Hardware-in-loop testing approaches reduce testing timelines and improve coverage when validating embedded software in automobile ECUs by utilizing modeling and simulation techniques.
This strategy is essential for use cases that are challenging to consistently reproduce in the field or a lab.
We’ll have a far higher probability of deploying an effective system after it’s eventually integrated if you simulate sensors, mechanical parts, and actuators to connect all the ECU inputs and outputs (I/O).
To do this, Hardware-in-loop testing can make use of electrical stimuli, representative real-time reactions, and functional use cases.
Hardware-in-loop testing is essential as autonomous driving and electric automobiles advance to guarantee dependability and safety.
Additionally, the growing interdependence and connectivity of systems and vehicle domains make it essential today.
This is so because each of these various components works in concert to produce essential car characteristics.
Why is Hardware-in-loop Testing Important & its Benefits?
Hardware-in-loop testing is mostly used to confirm and validate that automotive goods are performing as intended.
From an organizational perspective, this procedure lowers possible costs associated with errors or hardware damage while also speeding up product development.
Because this testing finds any problems with a component’s operation and enables engineers to fix them, it helps the entire product lifecycle development process.
They can alter things early on to reduce risks as much as feasible, whether they are functional or design-related. Vehicles are so designed to have as little possibility of malfunctions and safety risks as possible.
Benefits of Hardware-in-loop testing
Cost – HIL testing is less expensive and requires less maintenance than power lab testing. It also carries no risk of equipment damage.
Safety- There is no chance of destroying tools or putting people in danger when doing tests in a simulated setting.
Fidelity- It is guaranteed that the controller evaluated on HIL will function just as well when linked to actual physical equipment by using a high-fidelity real-time simulation running on an FPGA.
Flexibility- Wide-ranging scenario testing, real-time parameter adjustment, and testing under problematic situations can all be done in a virtual environment without the hazards that come with testing in a power lab.
Automation- To gather data without requiring supervision, an infinite number of automated test scripts can be written and left to run for a few days or overnight.
Speed – Continuous testing, which is the foundation of an agile methodology, enables prompt feedback on modifications made to the control software and prompt corrections if performance issues arise.
Time- Time can be saved during setup and construction, allowing the product to reach the market sooner.
What are the Challenges Faced in HIL Testing of an Automotive System
Automobile system development requires HIL (Hardware-in-the-Loop) testing, which is essential but not without its difficulties. In HIL testing automotive systems, the following are some of the main obstacles encountered:
Hardware and Software Integration:
- The smooth and compatible integration of a motor controller with other car systems and parts presents difficulties.
- For hardware integration and testing, Vector’s dSPACE SCALEXIO or VT system can be used to ensure that the motor controller, sensors (like position sensors), actuators (like electric motors), and communication networks (like CAN bus) are all properly communicating with one another.
Realistic Simulation:
- It needs precise and lifelike simulations to mimic the electric motor’s dynamic behavior.
- Engineers may develop high-fidelity simulations that take into account motor control methods, motor characteristics, and environmental elements like temperature and load fluctuations by combining MATLAB/Simulink with Simscape Power Systems.
- These simulations mimic the dynamic reactions and motor properties of the real environment.
Model Complexity:
- Complex mathematical models for feedback control loops, safety devices, and motor control algorithms are used in automotive motor controllers.
- Robust hardware-in-the-loop simulation systems, such as dSPACE SCALEXIO or NI VeriStand, that can execute high-fidelity motor control models with minimal latency, are required to handle the complexity of these models while preserving real-time performance.
Timing and Synchronization:
- Accurate testing depends on achieving perfect timing and synchronization between the Motor Controller, actuators (such as electric motors), sensors (like position sensors), and simulation models.
Data Acquisition and Signal Conditioning:
- Reliable data acquisition systems are necessary for the collection and processing of data from a variety of sensors, including temperature, current, and location sensors.
- Engineers may gather and condition sensor signals with high precision and low latency using systems like NI CompactDAQ or dSPACE DS4301, which offer trustworthy feedback for testing and validation.
Test Case Design and Coverage:
- Creating thorough test cases requires addressing a range of failure scenarios, motor control approaches, and operating environments.
- Model-based testing tools, such as dSPACE AutomationDesk or Simulink Test in MATLAB/Simulink, make it easier to create and run test cases that adhere to model standards.
- By taking into account various control modes, load situations, and failure scenarios, these tools provide comprehensive test coverage.
Hardware Fault Emulation:
- To assess the Motor Controller’s fault detection and reaction procedures, it is essential to replicate real-world hardware malfunctions or motor failure scenarios.
- Engineers can introduce errors, such as actuator malfunctions or sensor malfunctions, into the HIL test setup with the help of available tools.
- This makes it possible to replicate actual fault scenarios and confirm that the Motor Controller can manage errors and guarantee safe operation.
Cost and Resource Constraints:
- Setting up an effective HIL testing environment involves managing cost and resource constraints.
- This includes acquiring specialized hardware, software licenses, and skilled personnel.
- Organizations must carefully allocate resources, including HIL simulation platforms, data acquisition systems, and fault emulation units, to meet testing requirements within budget limitations.
Hardware-In-Loop Testing In Automotive Market Size And Forecast
Grand View Research estimates that the global hardware-in-the-loop market will reach a value of USD 665.4 million in 2023 and will grow at a compound annual growth rate (CAGR) of 11.1% between 2024 and 2030.
An essential component of modern engineering and technological development is the Hardware-in-the-Loop (HIL) market, with its sophisticated simulation environment for complicated system testing and validation.
Hardware-in-loop simulation mixes virtual models with real-world elements like sensors and actuators in a controlled environment to accurately mimic real-world scenarios.
Hardware-in-loop Testing use cases across industries
Automotive
HIL testing is widely used in sectors where complex system development and validation are essential. The automotive industry is one of the main sectors where HIL testing is frequently used.
HIL testing is crucial in the automotive engineering field to verify the operation of electronic control units (ECUs) and their interface with various car subsystems.
Without the requirement for actual prototypes, it enables engineers to model a broad range of driving scenarios, meteorological conditions, and problem states.
This shortens the time and expense of physical testing while accelerating the development process and guaranteeing the dependability and safety of automotive systems.
Aerospace
Other industries, including the aerospace industry, also use HIL testing. It is used to test the functionality and efficacy of communication systems, flight control, and avionics.
By using HIL testing, engineers may evaluate how well these systems work under a variety of flight conditions, disruptions, and failure scenarios.
By aiding in the early discovery and correction of any issues, it does this to help assure the safety and dependability of aviation systems.
Energy
The power systems and energy sectors also depend heavily on HIL testing. This method is used to verify the efficiency and stability of power-producing equipment, electrical grids, and renewable energy systems.
By modeling component behavior and testing the system’s response to various load scenarios, high-integrity load (HIL) testing helps power systems operate more reliably and efficiently.
Conclusion
The automobile sector may test its solutions ahead of time, even before the target platform is complete, thanks to hardware-in-loop testing.
Engineers can evaluate the functionality of components in simulated settings and fix any flaws found by using techniques such as HIL testing.
By taking care of these problems, they may guarantee that automobiles operate by safety regulations and lower the possibility of accidents involving safety on the roads that people use regularly.
Logic Fruit Technologies has developed robust IPs for these communication protocols, offering reliable solutions that enhance the efficiency of HIL testing by providing seamless integration and simulation of real-world automotive communication.
HIL testing ensures that ECUs communicate seamlessly with various subsystems, including sensors, actuators, and vehicle communication networks such as LIN, CAN, and FlexRay.